Unmatched Excellence in Best CNC Metal from Leading Chinese Manufacturers
In the realm of modern manufacturing, CNC metal machining has emerged as a cornerstone of precision engineering, particularly among leading Chinese manufacturers. According to a recent industry report by Grand View Research, the global CNC machine market is projected to reach USD 100 billion by 2025, with a significant portion driven by advancements in metal machining technologies. The growing demand for high-quality CNC metal products across various sectors, including automotive, aerospace, and electronics, underscores the necessity for unmatched excellence in production capabilities.
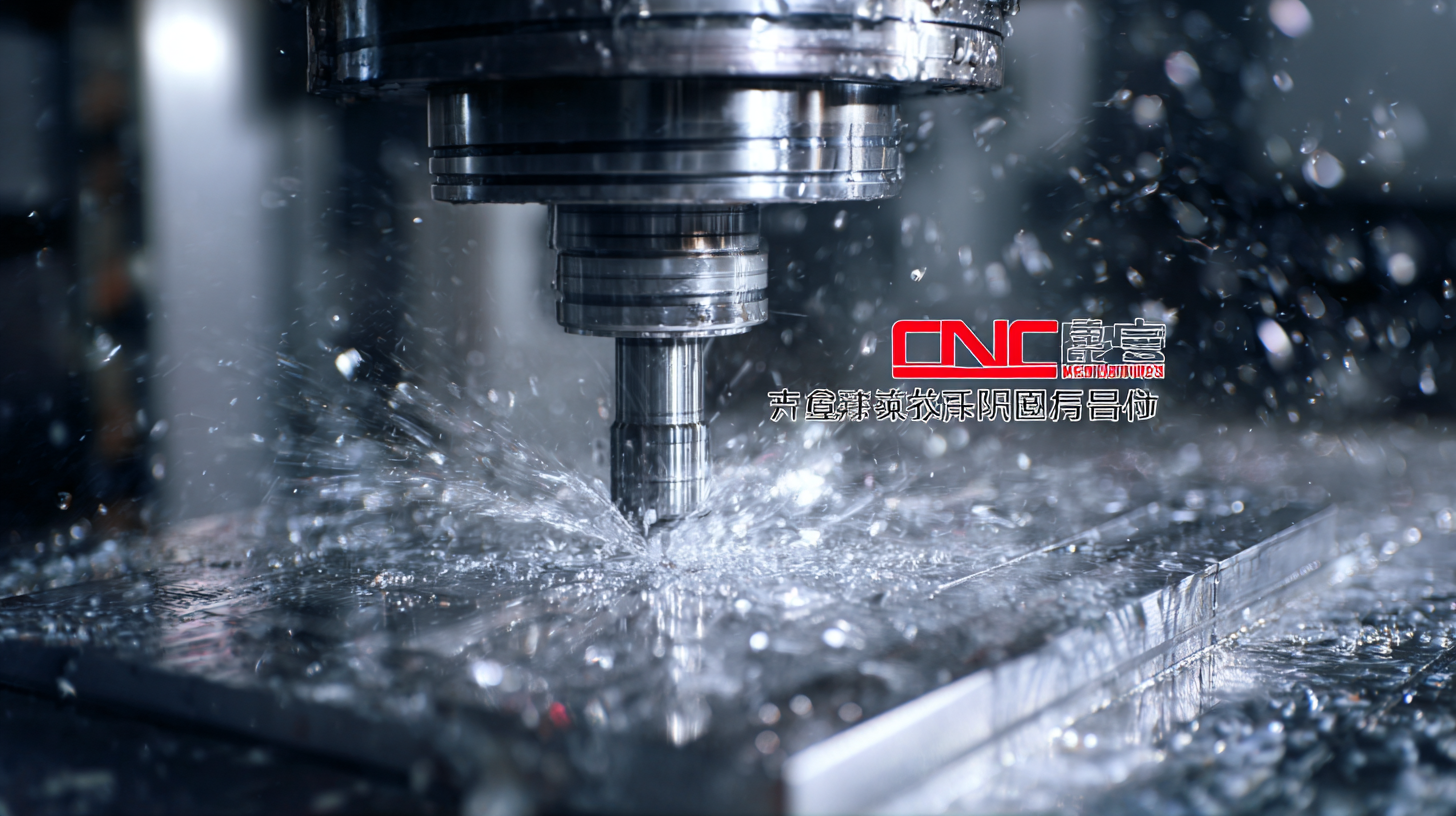
However, despite the remarkable technological progress, challenges persist in optimizing efficiency, ensuring quality control, and addressing supply chain complexities. This blog will explore these critical issues and highlight how esteemed Chinese manufacturers are overcoming obstacles to deliver superior CNC metal solutions to the global market.
Advancements in CNC Machining Technologies in China: Key Trends and Innovations
In recent years, China has emerged as a leader in CNC machining technologies, driven by significant advancements that are reshaping the industry. The global CNC machine market is poised for substantial growth, projected to increase from $101.22 billion in 2025 to $195.59 billion by 2032, reflecting a compound annual growth rate (CAGR) of 9.9%. This surge is fueled by innovations that enhance precision, reduce waste, and improve overall efficiency, aligning with the global push towards a more sustainable manufacturing ecosystem.
One of the key trends in China's CNC machining sector is the integration of advanced technologies such as artificial intelligence (AI), the Internet of Things (IoT), and big data analytics. These technologies not only streamline production processes but also revolutionize supply chain management, fostering a circular economy that minimizes environmental impact. As manufacturers adopt these cutting-edge solutions, they are better equipped to respond to changing market demands while championing sustainability efforts. The emphasis on precision tools and enhanced manufacturing methodologies positions these companies at the forefront of technological evolution, making them invaluable players in the global market landscape.
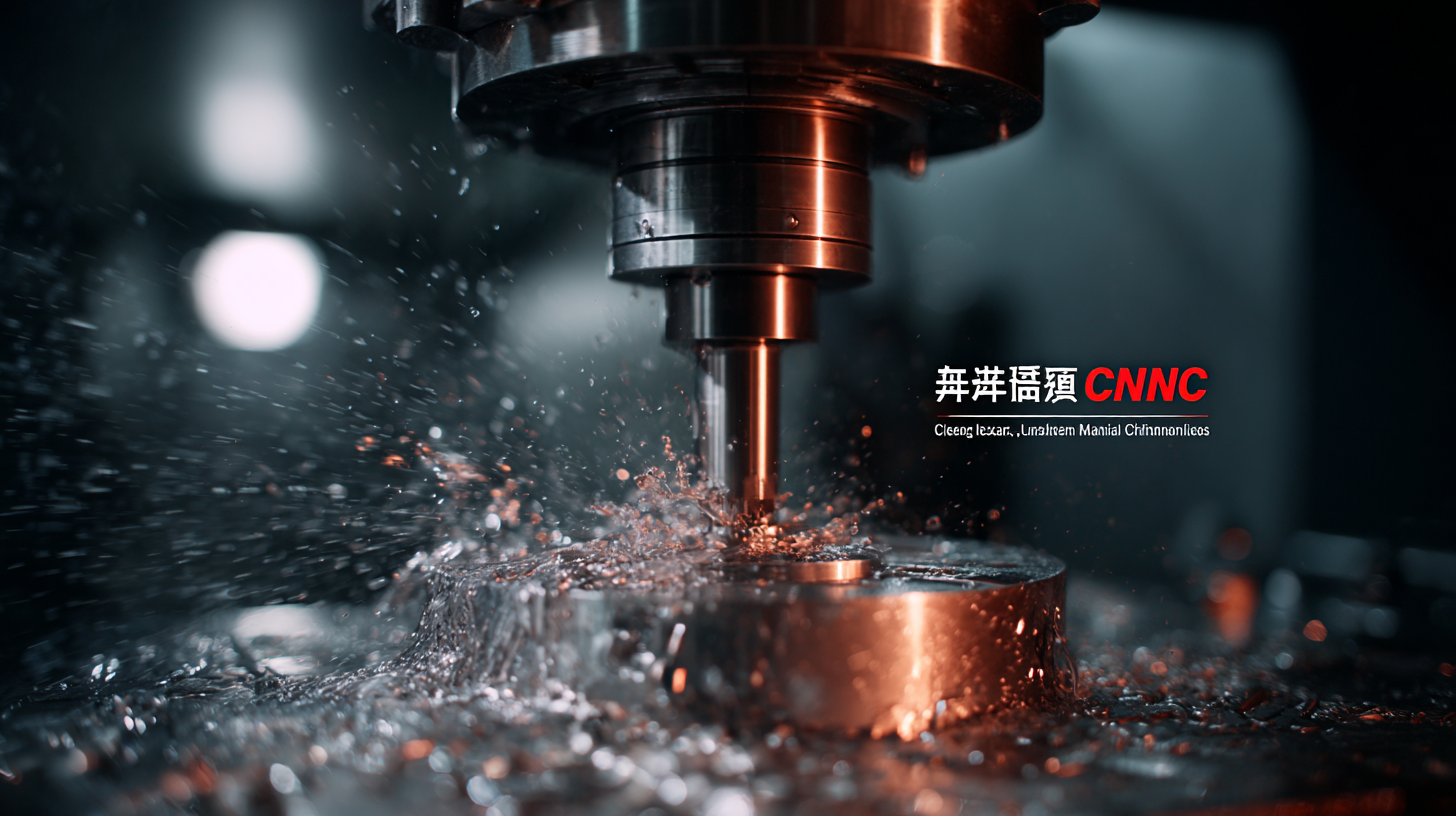
Market Analysis: The Competitive Edge of Leading Chinese Manufacturers in CNC Metal Fabrication
The CNC metal fabrication market is witnessing unprecedented growth, driven by the rise of automation in manufacturing processes. Leading Chinese manufacturers are at the forefront of this transformation, leveraging advanced CNC technologies to boost efficiency and maintain a competitive edge. As industries worldwide increasingly adopt CNC machining, the demand for precise and high-quality metal components is skyrocketing. This trend not only underscores the importance of innovation but also highlights China's dominion in meeting global market needs.
Market analysis reveals that the Asia-Pacific region, particularly China, plays a pivotal role in shaping the CNC metal fabrication landscape. With a significant market share, Chinese manufacturers are capitalizing on state-of-the-art machinery and skilled labor to produce a diverse range of products, from simple parts to complex assemblies. Their ability to combine cost-effectiveness with superior quality positions them favorably against competitors across the globe. As such, the trajectory of this market suggests that the influence of leading Chinese manufacturers will only expand, reinforcing their status as key players in the industry.
Market Analysis: The Competitive Edge of Leading Chinese Manufacturers in CNC Metal Fabrication
This bar chart illustrates the market share distribution among various CNC metal fabrication sectors in China. The data represents the competitive edge of leading manufacturers in the industry, highlighting their focus on different areas of CNC metal production.
Top CNC Metal Products: Performance Metrics and Quality Standards from Chinese Manufacturers
When it comes to CNC metal products, the performance metrics and quality standards set by leading Chinese manufacturers are nothing short of exceptional. As the demand for precision machinery components continues to rise globally, the latest advancements in technology are shaping the landscape of CNC machining. With the capability to produce high-quality metal parts that meet stringent specifications, these manufacturers leverage state-of-the-art equipment and techniques, ensuring that surface finish and dimensional accuracy are maintained to the highest standards.
One notable trend is the growing emphasis on in-process monitoring strategies in metal forming. Innovations in measurement methods allow for precise control of various parameters such as force, temperature, and geometry during fabrication. This ensures that finished products, such as impellers for pumps, achieve optimal performance and efficiency.
Additionally, the expanding metal processing machine market further highlights the increasing significance of quality assurance in production, as manufacturers strive to meet the evolving needs of industries relying on advanced CNC machining technologies. The ongoing commitment to excellence from Chinese manufacturers solidifies their position as global leaders in the field, making them invaluable partners for companies seeking reliable and high-performance metal products.
Supply Chain Efficiency: How Leading Manufacturers Optimize Production Processes in CNC Machining
In the competitive landscape of CNC machining, supply chain efficiency serves as a critical factor for success among leading manufacturers in China. These companies utilize advanced technologies and strategic partnerships to streamline their production processes, ensuring that materials flow seamlessly from suppliers to the manufacturing floor. By implementing just-in-time (JIT) inventory systems, they minimize excess stock and reduce waste, enabling them to respond swiftly to changing market demands without sacrificing quality.
Moreover, leading Chinese manufacturers are harnessing data analytics and automation to optimize their operations further. By analyzing production metrics and lead times, they can identify bottlenecks and areas for improvement, allowing for real-time adjustments to be made. This proactive approach not only enhances productivity but also fosters stronger collaboration within the supply chain, ensuring that every component of the manufacturing process aligns perfectly. As a result, these manufacturers can offer unmatched excellence in CNC metal products while maintaining a cost-effective and efficient production model.
Unmatched Excellence in Best CNC Metal from Leading Chinese Manufacturers
Manufacturer Type | Production Capacity (Units/Month) | Average Lead Time (Days) | Material Types | Quality Certifications |
---|---|---|---|---|
Precision CNC Machining | 5000 | 15 | Aluminum, Steel, Titanium | ISO 9001, ISO 13485 |
Custom CNC Fabrication | 3000 | 20 | Brass, Copper, Plastic | AS9100, ISO 9001 |
Automotive CNC Parts | 8000 | 30 | High-Strength Steel, Aluminum Alloys | IATF 16949, ISO 9001 |
Industrial CNC Components | 4000 | 25 | Carbon Steel, Stainless Steel | ISO 9001, ISO 14001 |
Future Outlook: Growth Projections for the CNC Metal Industry in China and Global Impact
The CNC metal industry in China is poised for significant growth, with projections estimating a compound annual growth rate (CAGR) of 8.5% from 2023 to 2028. As the demand for precision components escalates across various sectors, including aerospace, automotive, and electronics, China’s CNC metal manufacturers are stepping up to meet global standards. Reports indicate that the global market for CNC machining is expected to reach approximately $100 billion by 2025, with a substantial share attributed to Chinese producers who are now leading in both output and technological advancements.
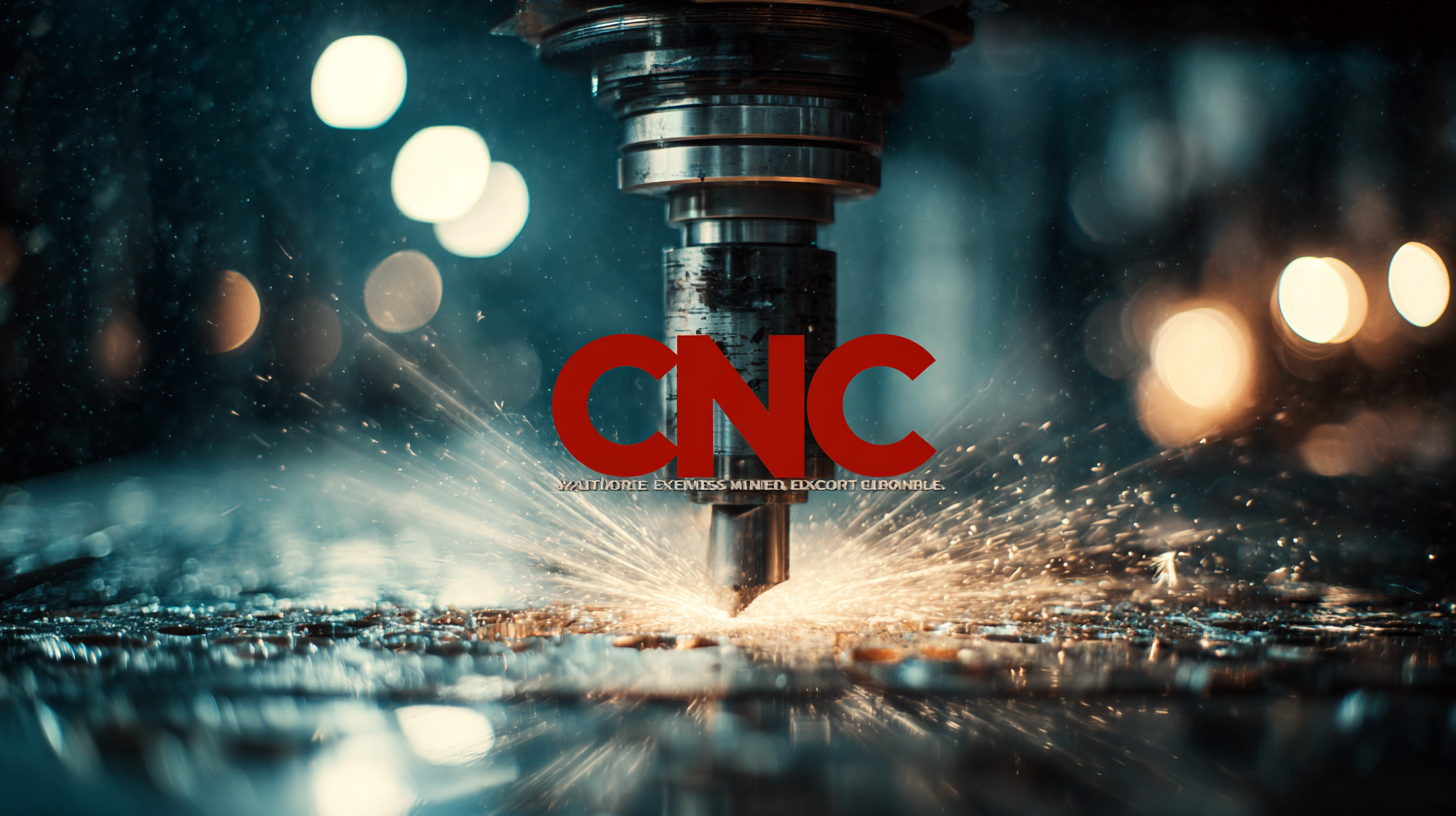
Furthermore, the integration of Industry 4.0 practices, such as advanced automation and data analytics, is transforming the landscape for CNC metal machining in China. According to a recent study by Mordor Intelligence, nearly 60% of manufacturers in China are adopting smart manufacturing technologies, which not only enhance efficiency but also improve product quality and reduce lead times. This trend is crucial as Chinese manufacturers strive to gain a competitive edge in the global marketplace, ultimately impacting supply chains and production dynamics worldwide. With continued investment in technology and innovation, the future outlook for the CNC metal industry in China remains robust, poised to influence global manufacturing practices significantly.